In June 2014 Jamie Woods of R & J Seafoods contacted Peter Kettell of PJK Consultancy & Training for a solution to provide traceability and stock control for their fish block factory in Grimsby, England.
Following initial telephone discussions an outline specification and budget estimate was produced. Following receipt of this outline PJK Consultancy were invited to visit site to conduct a site survey, with the intent to provide a more detailed specification and actual project quotation.
At that time, the R & J operation took place on the premises of Albert Darnell Ltd, a Seafood processor. R & J purchased many of the secondary products from Albert Darnell, as well as additional purchases from other suppliers. These secondary products are typically offcuts of several types of fish, frames, loins, tails etc.
R & J Seafoods process these products into fish mince blocks and fish blocks (both Frozen).
Some of the products are purchased fresh, some frozen. The frozen products need to be de-frosted prior to processing.
There are two processes, the first consists of mincing, until a fish mince is produced. This is then portioned into trays and frozen for dispatch as 7.5kg mince blocks. The second process is the same except the fish is not minced. It is simply portioned into 7.5kg blocks and frozen.
The blocks are then palletised and sold to further processors.
It is a simple operation, but R & J Seafoods were being pushed to improve the traceability of their products.
Having an agreed specification, Peter contacted Daniel Simonavicius of Danius Labs for an estimate on the software element. Peter and Daniel had worked together successfully for many years.
It was decided that although the R & J application appeared straight forward, it did present an opportunity (being a complete factory solution) to create the foundation for a full factory production management system. As such a new company “Xtrace systems” with a software product “xTrace.app” was born.
By taking advantage of having a customer, where there was no requirement to link to existing hardware or software. Daniel decided to create a new system architecture, based on his previous experience but utilising state of the art programming techniques and not having to consider legacy applications.
Microsoft SQL server was chosen as the system database, and the .net framework together with Dev Express software development tools to implement the project.
There would be an office-based client program for datafile management and reporting, and a touch-oriented terminal client for use on industrial shop floor PC terminals.
As transactions would be mostly at pallet level, it was calculated that the database size would stay small, with a small number of transactions. Due to this, the database was implemented on the free version SQL Server express.
Having been awarded the contract in February 2015, the partnership of Peter and Daniel set about developing the product. Peter writing the specification, Daniel developing the software. Testing was a joint effort. The initial implementation was conducted close to schedule and as is customary for such systems, new functionality requirements came thick and fast. Partly due to circumstances not covered by the specification, and partly based upon innovative ideas R & J developed, having seen what the system could do.
The initial implementation included the following functionality:
- Intake Data capture (linked to a pallet scale and label printer)
- Frozen stock (Raw Material)
- Fresh Stock
- De-Frosting stock
- Mincing (Linked to a pallet scale, bar code scanner and label printer)
- Work in Progress (WIP stock)
- Packing
- Palletising (Linked to a pallet scale and label printer)
- Mincing Yield
- Packing Yield
- Overall Batch Yield
- Frozen Stock (Finished Goods)
- Despatch (linked to a bar code scanner, label printer and report printer)
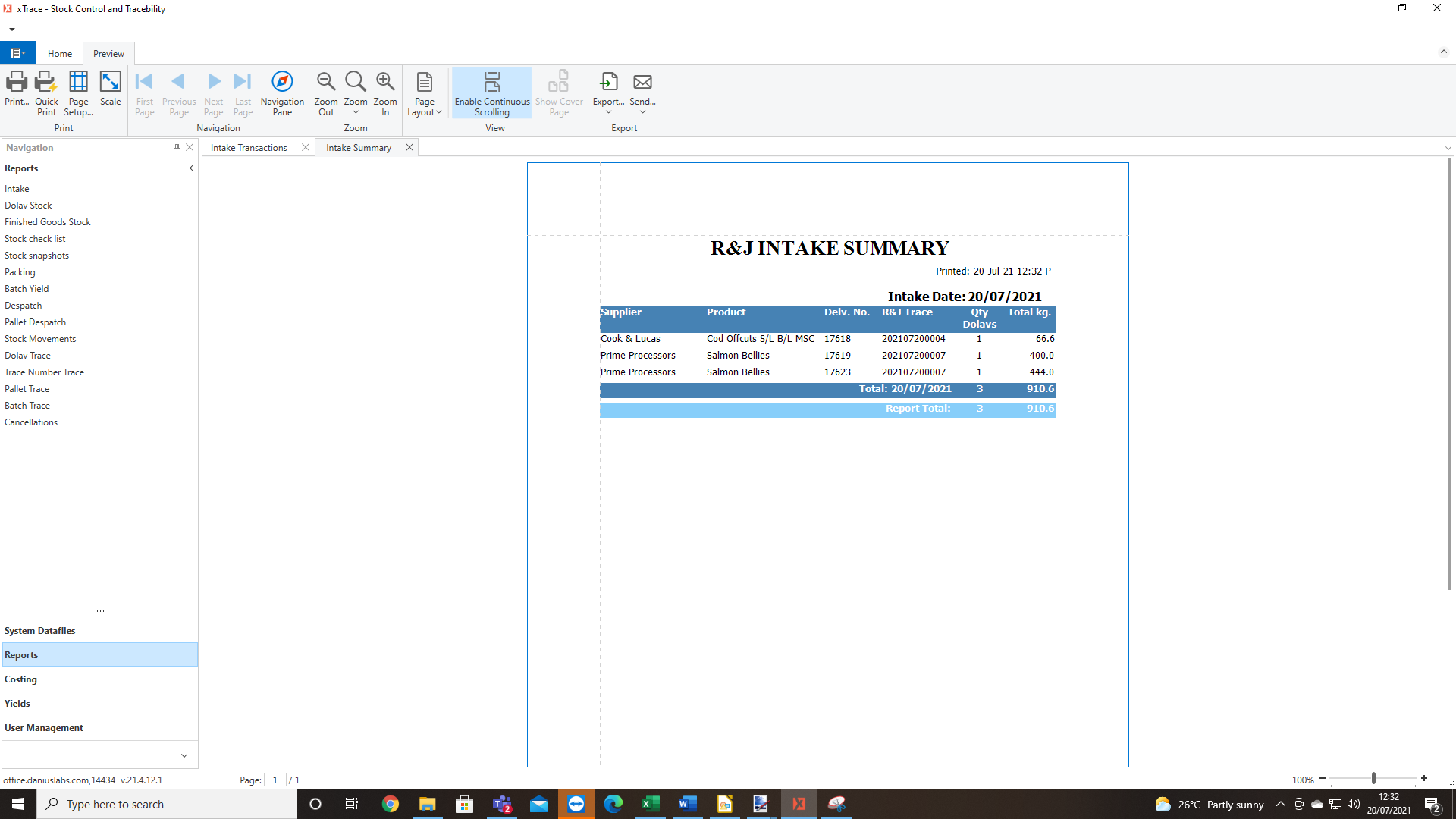
Example of Intake Report
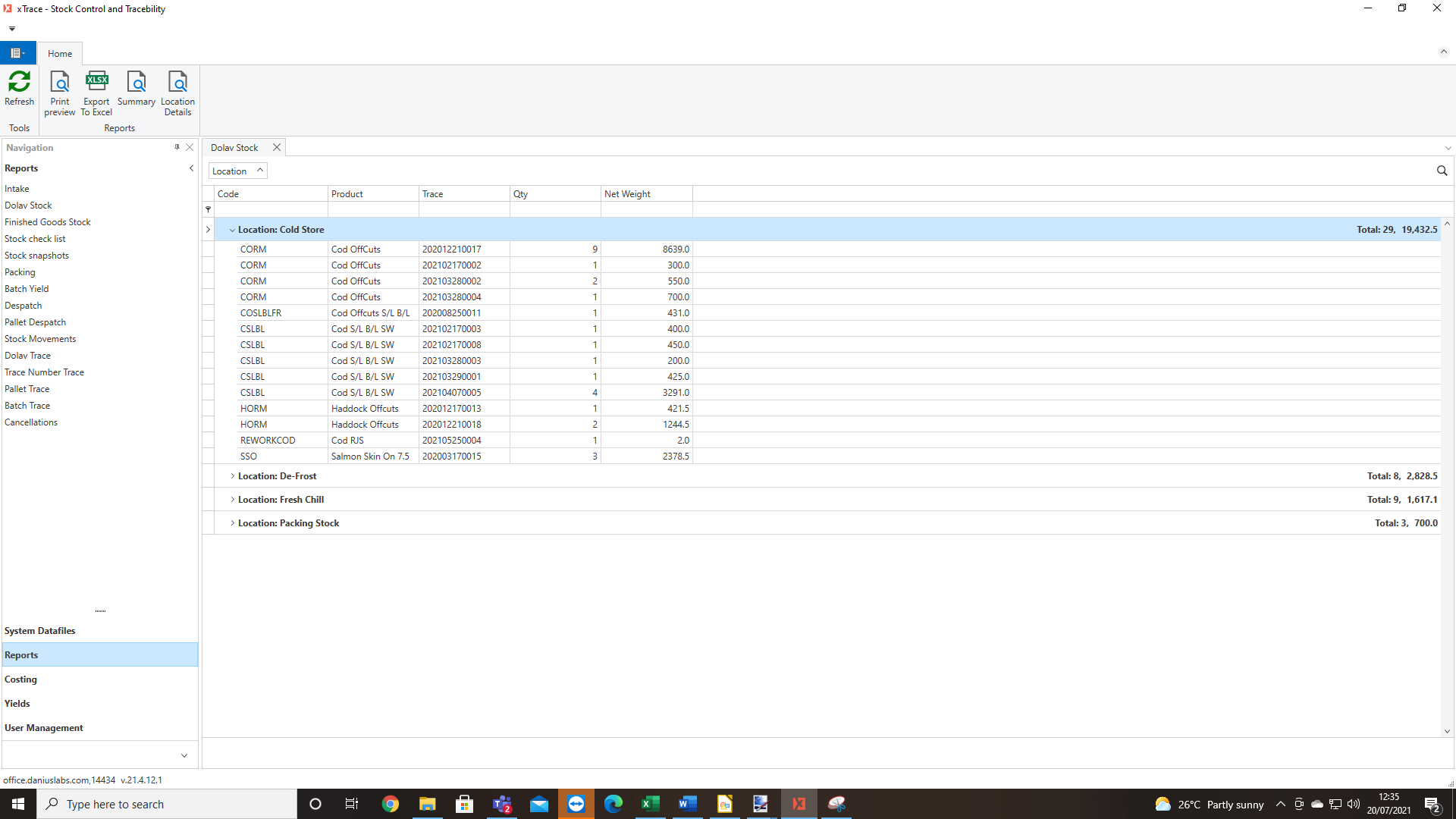
Example of Stock Grid
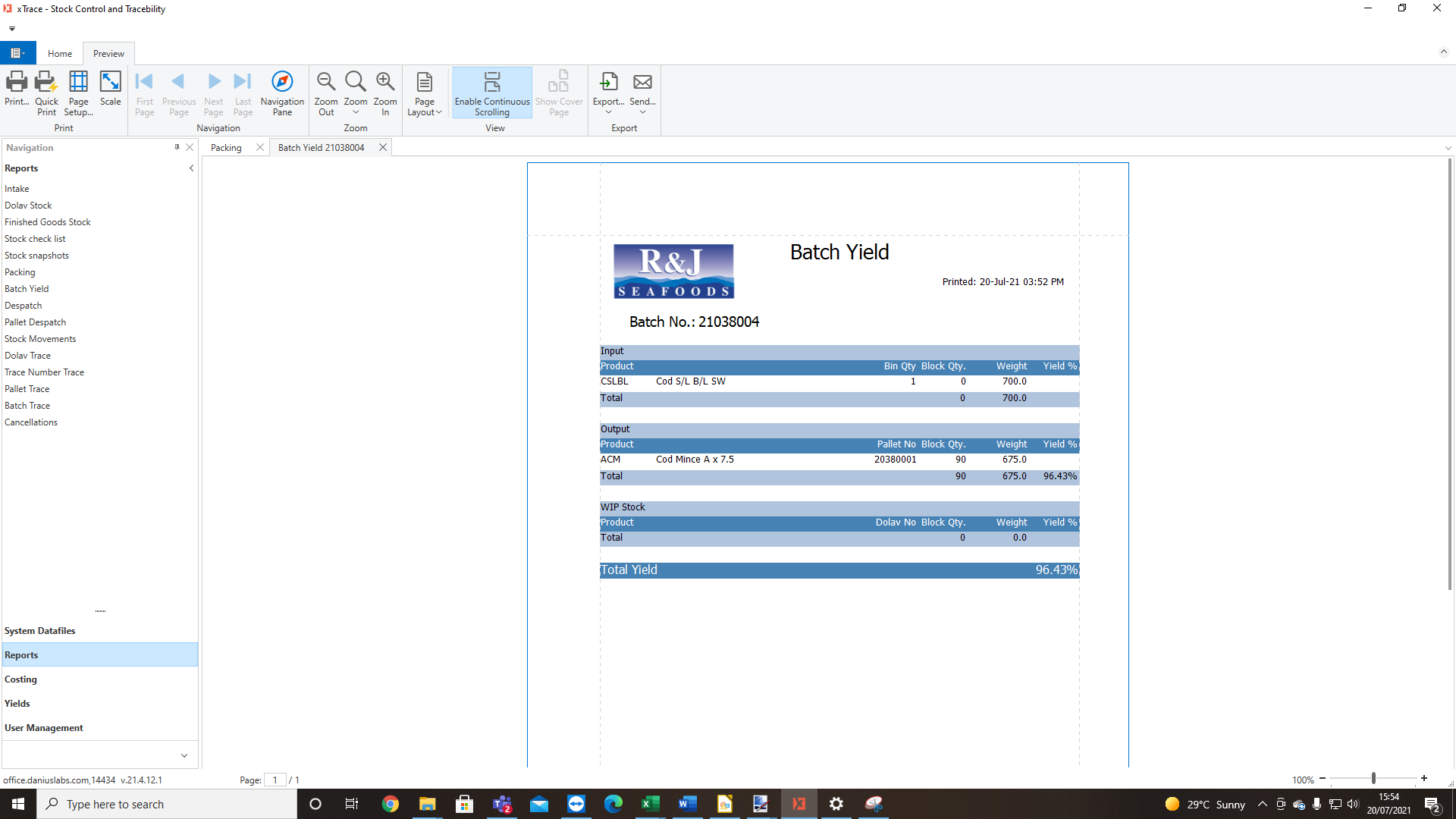
Example of Batch Yield Report
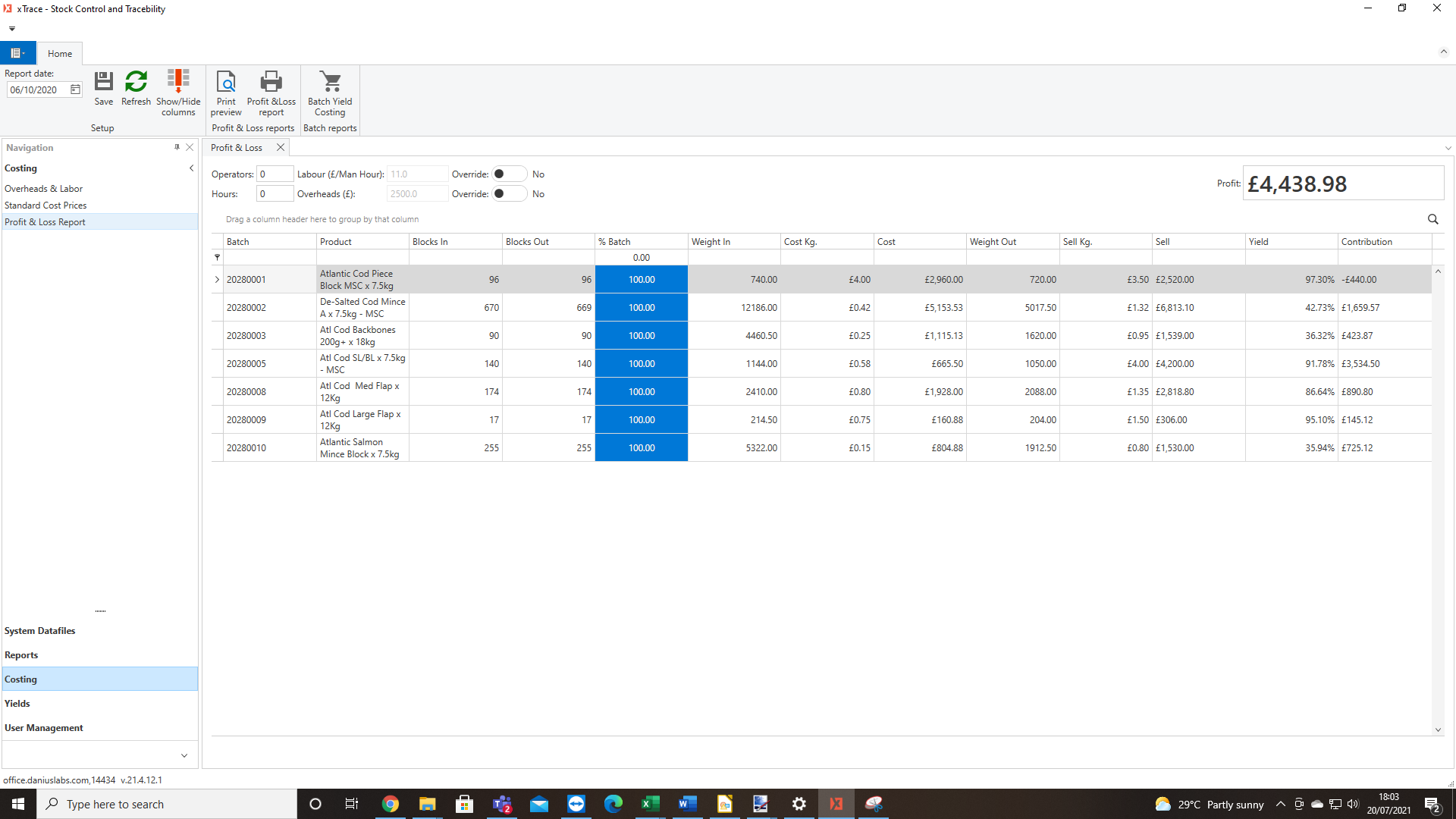
Example of Profit & Loss Report
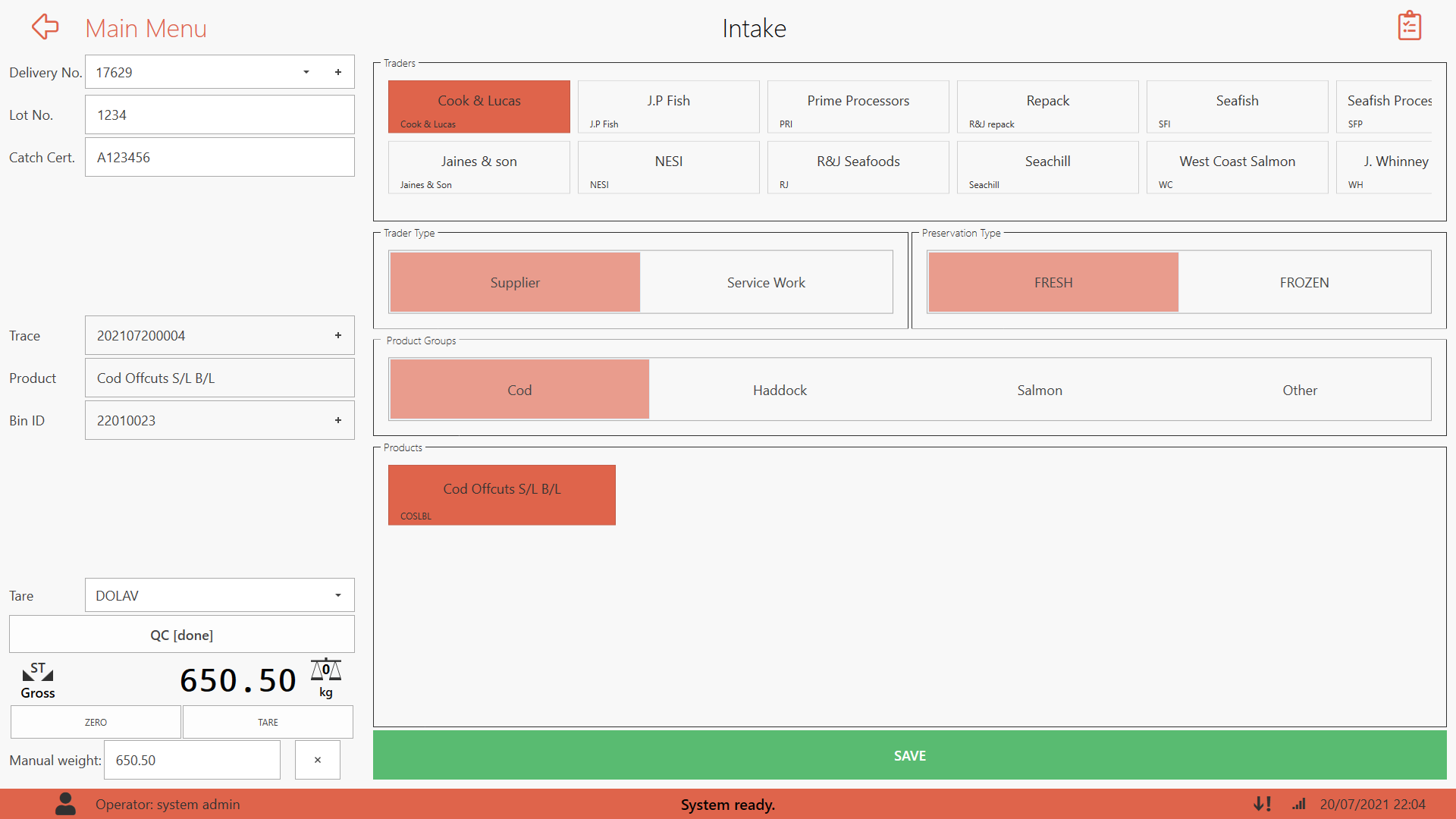
Intake Data Capture Form
Very quickly quality attributes data collection was added at the intake and despatch stations, with a QC release function in case quality is not recorded at time of weighing.
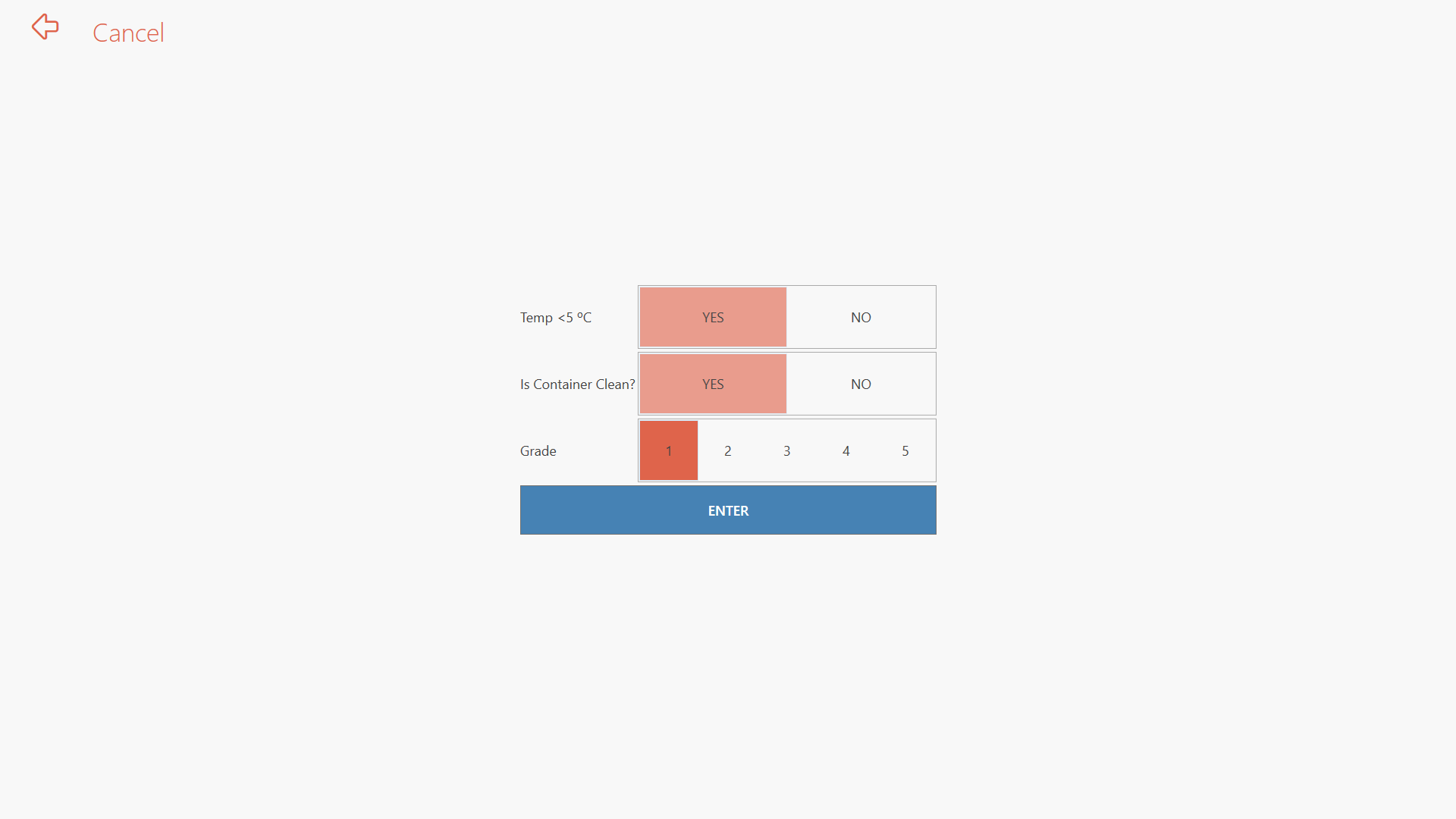
Quality Attributes at Intake.
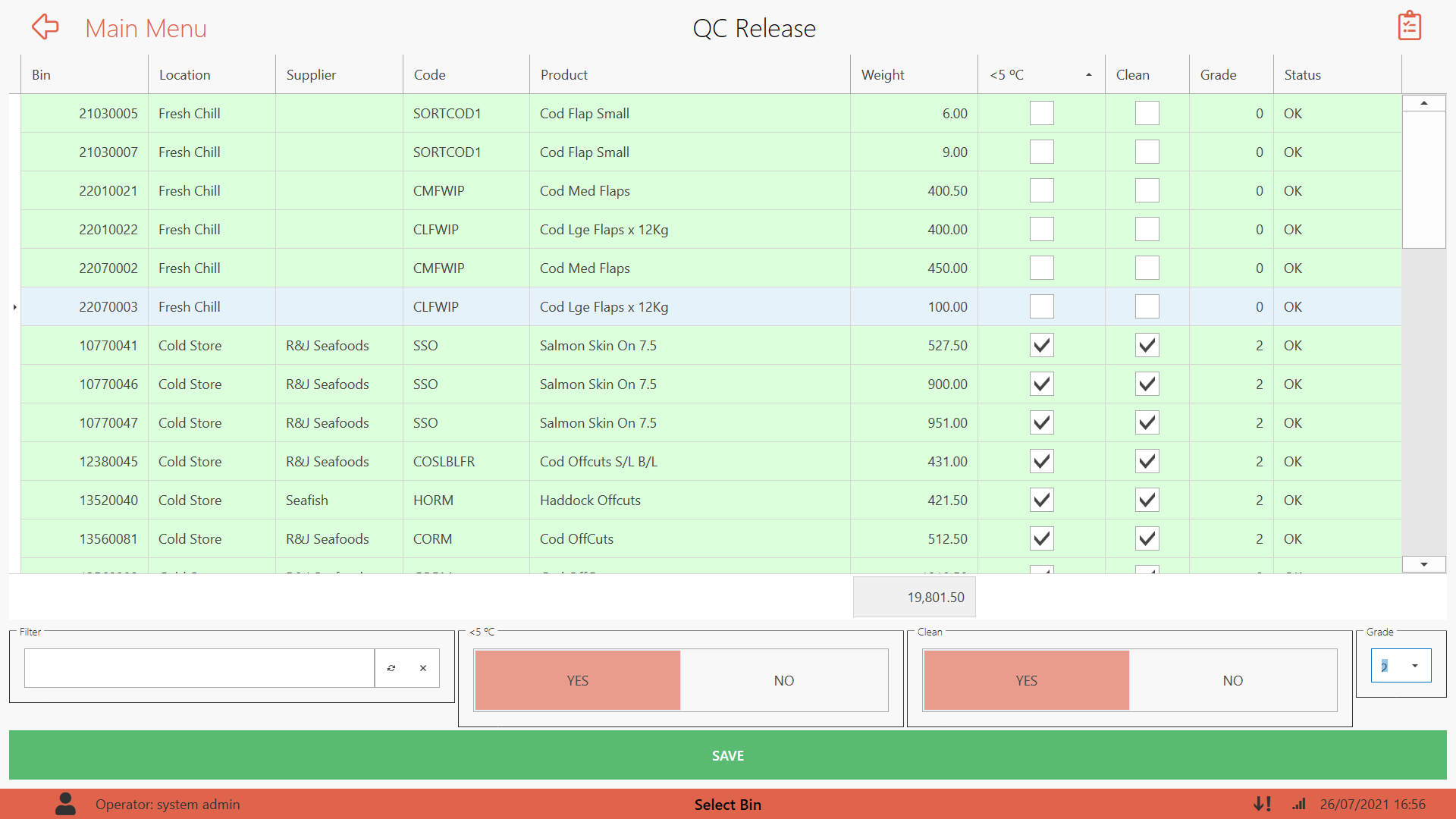
In 2018 R & J Seafoods moved to new premises in Grimsby, with an opportunity for increased on site cold store holding. At this time, the system had to be moved onto a new server and Daniel assisted with the database move and re-implementation of the system.
Following the move R & J asked if the system could be used to produce a daily profit and loss report. As costing was not part of the original system this was quite a major change and after being awarded the contract it took several months of testing and re-writing before the project was accepted and implemented into the live system in early 2019.
In 2021 Daniel and Peter formed Xtrace Systems. One of the first tasks was to update R & J Seafoods to be a hybrid system between the current system and then new xTrace.app.
Other R & J projects under discussion are integration with 3rd Party cold stores, filling control for 7.5kg trays and in line check weighing for finished products.
On initial installation we had a few issues where the delivered solution did not match the way our operators worked. Xtrace stuck with it though, and after a few functionality adjustments, we quickly became very reliant on the information it was giving us. The support from Daniel and Peter has never been anything other than first class. Any issues we have had, have been quickly sorted and they respond promptly to new requests, we will certainly be expanding the system in the future.
Jamie Woods of R & J Seafoods